JTC can now halve the time needed to track and document construction progress on its projects, thanks to the adoption of 360° reality capture technology. SEAC finds out more about this digital solution and the benefits it brings to the industry.
As the government agency in charge of Singapore’s industrial development, JTC is setting the pace for digital transformation in the construction industry with the adoption of advanced technologies. One such innovation is a 360° reality capture solution to be employed in more than 30 JTC developments and JTC-managed public infrastructure projects.
This initiative, in collaboration with US-based technology provider OpenSpace and its local partners Ace Peripheral and Asia Infrastructure Solutions, was rolled out in March 2024. The innovative system uses 360° photogrammetry technology to document changes at project sites, instead of taking still photos and manually uploading them.
Additionally, the system’s integration with JTC’s connected data environment – called ‘Optimus’ – allows data from the technology to be tapped to improve project quality and safety.
According to John Kiong, director, Future of Building and Infrastructure Division at JTC, the system is available to all parties in the value chain – from project managers and consultants to contractors and subcontractors. Although the 360° reality capture solution is intuitive to use, training is provided to all users via onboarding training sessions, manuals, refresher courses, periodic clinic sessions and WhatsApp support. By rolling out the solution across its value chain, JTC aims to reduce adoption barriers and foster industry-wide productivity gains.
Mr Kiong shared some of the projects where JTC and its partners have used the 360° reality capture technology. These include:
-
Construction of Punggol Digital District. Project staff used the technology for site progress update, general communication of site status and virtual TOP (Temporary Occupation Permit) inspection.
-
Demolition works for Toa Payoh Integrated Development. Site staff used the technology for safety observations and progress tracking.
-
Construction of Loyang North Substation. Project managers used the technology for progress tracking and safety monitoring.
-
Addition and alteration (A&A) works for a flatted factory at 28 Ayer Rajah Crescent. Site staff used the technology for progress tracking.
-
Phase 1 infrastructure works for Jurong Innovation District. The project team used the technology for virtual TOP inspection.
-
Road handover to LTA (Land Transport Authority). Project managers used the technology to conduct virtual inspection of 13 roads prior to their handover to LTA.
Significant improvements
Historically, documenting site progress through photography has been a tedious and time-consuming task. In contrast, the new system involves affixing a small 360° camera to the hard hat worn by staff, enabling seamless capture of the entire surroundings and every detail during a site walk. The resulting 360° photos are then uploaded to a web platform, which will be immediately accessible to all parties in the project’s value chain.
Moreover, the system is equipped with computer vision and artificial intelligence (AI) to automatically pin photo captures to floor plans, providing project management staff with an easy and intuitive way to visualise and document construction progress in real time. The platform’s timeline feature allows side-by-side comparison of 360° photos of the same location to track its progress.
Prior to implementing the technology, JTC conducted several trials and the results showed significant efficiency gains. Project teams saw a 60% reduction in time for site data collection and documentation, and a 50% decrease in time for data search, progress tracking and analysis. Furthermore, the system enabled time savings for site discussions of about 40% and a further 75% reduction in time for monthly site walks, primarily due to the elimination of travel to and from the site.
These savings underscore the transformative impact of the new system on project management, said Mr Kiong. The adoption also addresses the challenges in the construction industry such as a dwindling workforce and increasing competition for skilled labour.
JTC is currently tracking the performance of the system following its implementation in March. “So far, it has met expectations in automating time-consuming and manual tasks in site progress updates, communication of site status, as well as in virtual TOP inspections. This enables users to concentrate on higher-level work that brings greater value to construction projects or developments, such as problem-solving and more accurate planning,” said Mr Kiong.
Digital future
Apart from reality capture technology, JTC has embraced robotic solutions to boost site productivity, safety and quality on its projects. For example, at JTC’s Bulim Square facility in the Jurong Innovation District, its contractor Great Resources (M&E) Contractor Pte Ltd has deployed a drilling and anchoring robot for prefab MEP (mechanical, electrical and plumbing) installation works where the ceiling was more than 4.8 m high.
“We were able to achieve a 40% reduction in labour costs as fewer workers are needed for drilling tasks. Drilling times have also been reduced by 50%, shortening project timelines and increasing overall productivity. More importantly, there are fewer work-at-height risks and less worker fatigue,” said Mr Kiong.
To help inspectors spot and report defects in roadside infrastructure within JTC’s industrial estates, JTC has also implemented an automated estate inspection system in estates in Singapore. The system taps AI and real-time machine vision to inspect defects on road surfaces and other roadside infrastructure in the estate. Inspectors perform estate inspections by mounting a smartphone with a full HD camera on a vehicle driven at a normal speed. The footage captured is uploaded and processed by an AI system hosted in the backend server, which identifies the defects and their location, grades their severity, and highlights those in need of repair. After the drive-through, the inspectors can verify the defects highlighted, and the system instantaneously generates a report with the details of the defects to facility managers for their action, streamlining the previous workflow where the latter had to wait at least a few days for the report.
Mr Kiong said the system can complete inspections in 60 minutes compared to the past where a manual inspection can take up to two days. “The extensive training of the AI models also allows a high accuracy rate of 90% to be achieved for estate inspections at one-north, and by using a slightly higher-end smartphone, the system can operate in low-light settings, providing the opportunity for night-time inspections,” he added.
Moving forward, JTC aims to drive innovation in the construction industry by piloting new technologies and playing a key role in facilitating change and encouraging its value chain partners to get on board with digital transformation.
With its role as the public sector’s Centre of Excellence for building and infrastructure projects, JTC is committed to driving productivity improvements in the construction industry through technology adoption and scaling up best practices. However, Mr Kiong assured that any new technology will be shared and encouraged among the industry. “As with the reality capture solution, by availing the [digital] platforms for our project managers and partners’ use, we allow them to see the benefits in improving productivity, reducing manpower on site, and reducing cost from delay and reworks. They will then be less hesitant to start using it in other projects,” he said.
All images: JTC
Note: This story has also been published in the Nov/Dec 2024 issue of SEAC (with more images). Click here to read it online or here to download the PDF file, on pages 32-35.
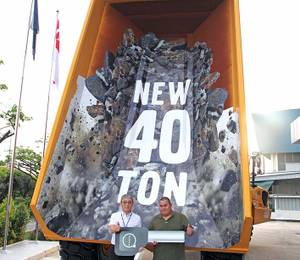
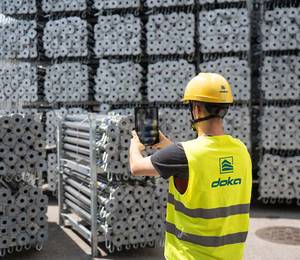
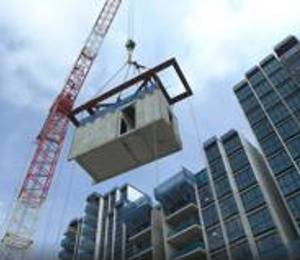
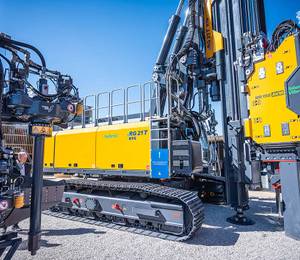
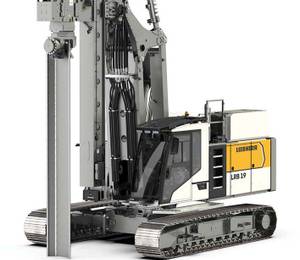
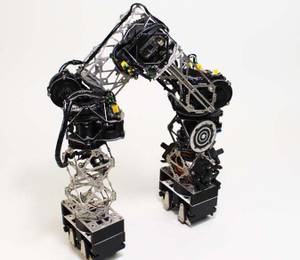
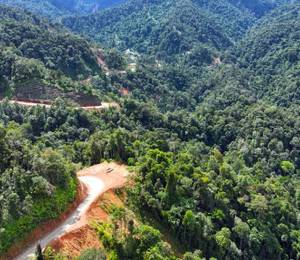